Description
Direct Metal Laser Sintering (DMLS) metal 3D printer, an open system designed for research that lets you define laser spot size, laser speed and power and precisely control printing paths. Allowing you to freely perform multiple tests on various types of alloys.
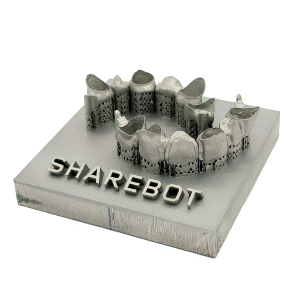
DENTAL
The possibility of using cobalt chrome powders combined with the speed and ease of use allows the dental laboratories to make restorations, crowns or a plate of copings in less than 1 hour
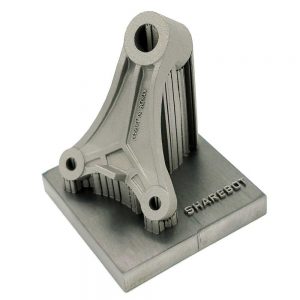
INDUSTRY
Small parts with incredible details can be easily prototyped and produced in a short time and without any particular difficulty. The extreme repeatability of the prints can guarantee the production of a series of pieces. Furthermore, the pieces produced are through a high-quality standard process
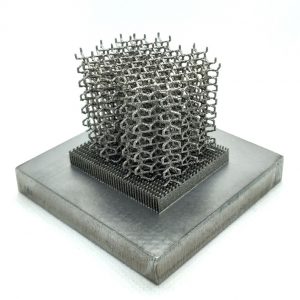
JEWELRY
MetalONE thanks to its reduced working chamber and the particular structure of the paper filters, it is also useful for the sector of additive jewelry and micro-objects. Its 250 Watt laser combined with a 10 micron layer and a 40 micron spot makes it possible to create particularly detailed objects in a short time
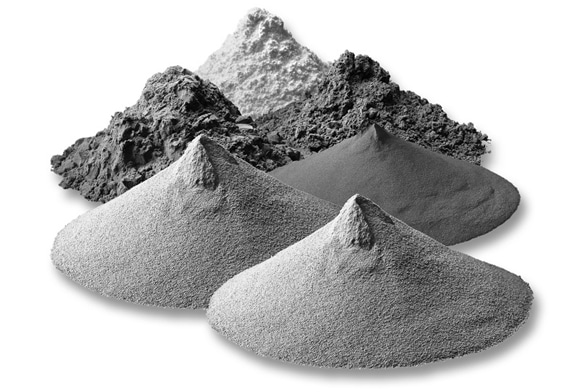
MATERIALS
Today the profiles for 316L steel and cobalt chrome are available. At the time of delivery we will also have available Titanium and Aluminum. Our R&D team and some universities are testing special powders and alloys that will be released and documented in the metalONE CLUB area. In that reserved area we will publish news, information and test results as well as useful information such as Quick Start, Manuals and software in order to access the area it is necessary to apply to metalone@sharebot.it
THE PROJECT
MetalONE started in 2015. During this period, Sharebot undertook the design of a thermoplastic powder sintering 3D printer, Sharebot SnowWhite. After dozens of installations of SnowWhites around the world, Sharebot has accumulated enough experience to move to a new project: Metal. Unlike the previous project, the new device varies in the powers involved and in the printing chamber designed to create and maintain a modified atmosphere. Despite having redesigned the software and the mechanics of the printer from scratch, the MetalONE project can be considered a direct descendant of the SLS SnowWhite project
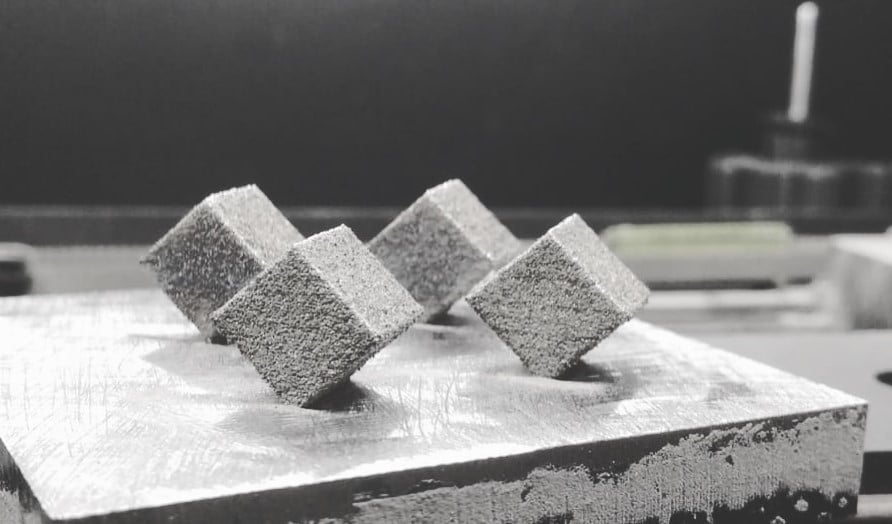
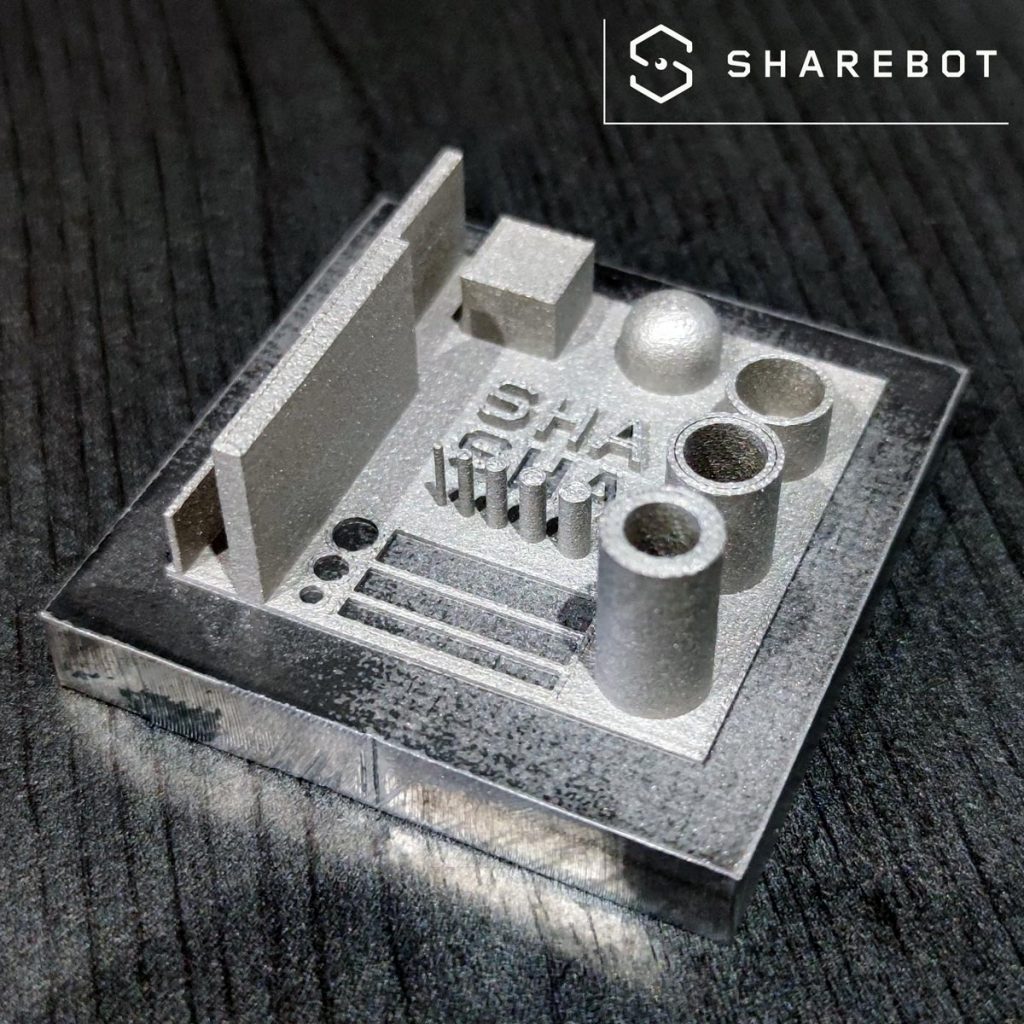
THE STORY
At the beginning of 2018, a team of engineers was created to design a metal 3D printer with innovative features. All aspects have been taken into consideration to obtain a reliable, economical, easy to use product with low running costs and completely transparent and open to the user in all its parameters. After various simulations and analyses, the project came to life with an innovative solution that meets the requirements.
After more than 12 months of work in March 2019, the first prototype and first prints were presented at the Parma during MECSPE 2019. Since then, every day various kind of prints are made to check the metallurgical properties of the objects and the quality of the same, as well as the sturdiness of the printer itself and the repeatability of the prints. The printer has all the process parameters available to the user which will be facilitated in the research and study of new materials and applications.
Till June 2019 several tests were made for a total of hundreds of hours of continuous work, then the first production batch of printers was launched.
MetalONE is currently undergoing an initial beta-testing phase with selected specific users that will help us profile the powders.
With an extremely attractive launch price, the pre-order phase has begun.
The printers will be delivered after the Formnext 2019.
Reviews
There are no reviews yet.